My snowcat buddy, Scott, and I are working on two Tucker projects somewhat simultaneously. This thread features the second machine, which we named "Snowzilla". The thread will follow the progress of the different parts of the project which includes various repairs and numerous modifications. I'll post updates periodically, but it will be a minimum of several months before it's complete. I hope you enjoy it.
In November of 2015 I saw a 1980 Tucker 1643 listed on ksl.com. Based on the listing description, I thought it was potentially a good buy and sent a PM to a new forum member whose screen name was fsdesign. He was looking for a snowcat and I thought this was an excellent candidate for his needs. He passed on it, and so I bought it.
In my opinion, if you need to carry more than four people and you’ll be operating in deep snow, the 1643 is the holy grail of backcountry access, rubber belted Tuckers. The thing is though, they’re comparatively rare. If a decent one becomes available at a reasonable price you have to be ready to jump and jump now, otherwise it will be gone. Here are some pics of the machine when I went to look at it.
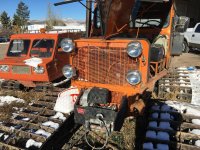
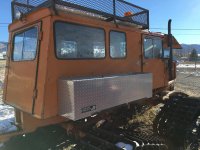
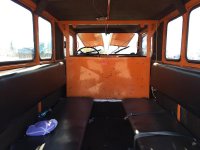
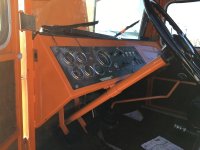
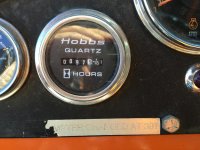
Pretty nice machine overall; it was originally owned by Pacific Gas and Electric. There was a placard indicating the hour meter had been changed at 397 hours and the new meter showed 97.1, so just under 500 hours. It was originally ordered as a 1543 per the data plate, and somewhere in it’s life the carriers and tracks had been upgraded to the longer 1600 series versions. SnoTrans sold it to the guy I was buying it from in 2002, and it had the long tracks on it then, so I suspect the upgrade was done during PG&E’s ownership. A couple of bonuses; the Tucker came with a factory installed Warn 8,000 LB winch, and the carriers had the damper wheel upgrade done to them. It had a nice, large rooftop carrier someone had added as well. There were a few repairs that I thought were poorly done, such as a patch on the top of the gas tank, and an ill fitting aftermarket electric fuel pump. But other than that - not bad at all. The paint was original and had 35 years worth of weathering and scratches.
When I was inspecting the machine, the gasoline smelled terrible and the engine had a miss in it. I attributed the miss to either poor fuel, or simply needing a tune up and didn’t think much of it. After buying it, I took it home and cleaned out the inside and then dropped it off at my snowcat buddy’s shop in SLC.
The first order of business was a tune up. The spark plugs looked to be nearly new so we left those alone, but new ignition wires, distributor cap and rotor were installed. And…no change to the miss. So we decided to rebuild the carburetor. In the process we found a significant amount of crud inside and thought that it certainly would run better after the rebuild. And…it didn’t. The next step was a compression check and we found zero compression on two cylinders! How do you have zero? Even if there were holes in the pistons you should see a temporary increase and then a drop. So, off with the valve covers and…the mystery was solved. We found two bent pushrods and two broken rocker arms. I called my “friendly" Dodge dealer and the parts guy only had books that went back to 1985, and he doubted he could get them anyway. Surprising to me, considering how many 318s Chrysler built during the sixties, seventies and eighties. Rather than get some cheap, made-in-China ones, we hit the salvage yards. Believe it or not, finding a 318 or 360 was not easy. Most yards have crushed their older vehicles and focus on newer models. Once the used parts were cleaned up and installed, we started the engine and it ran great. In the carburetor rebuilding process we decided to remove the factory manual choke cable and we installed an automatic choke instead.
Here are some photos of the bent pushrods and broken rocker arms. A couple things to note: For one thing how clean the parts are, indicating low usage and frequent oil changes. The other thing I’d mention is the straighter pushrod was actually much worse. So bad in fact it wouldn’t pull out of the cylinder head without straightening it somewhat.
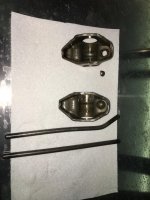
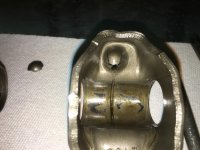
An obvious question is “How did the pushrods get bent and the rocker arms broken?” My understanding is one can bend pushrods at high RPMs if the valves float. But I don’t think that’s the case here. I suspect this sat for a long period of time, the affected valves were closed and they rusted shut. When someone went to start it, the pushrods bent and the rocker arms broke before the valves moved, but that’s really a semi-educated guess.
In November of 2015 I saw a 1980 Tucker 1643 listed on ksl.com. Based on the listing description, I thought it was potentially a good buy and sent a PM to a new forum member whose screen name was fsdesign. He was looking for a snowcat and I thought this was an excellent candidate for his needs. He passed on it, and so I bought it.
In my opinion, if you need to carry more than four people and you’ll be operating in deep snow, the 1643 is the holy grail of backcountry access, rubber belted Tuckers. The thing is though, they’re comparatively rare. If a decent one becomes available at a reasonable price you have to be ready to jump and jump now, otherwise it will be gone. Here are some pics of the machine when I went to look at it.
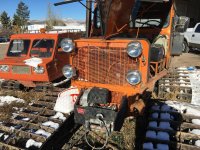
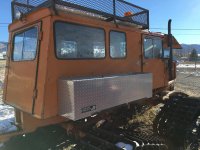
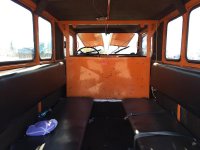
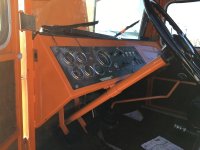
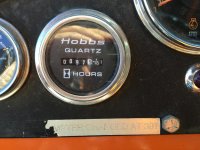
Pretty nice machine overall; it was originally owned by Pacific Gas and Electric. There was a placard indicating the hour meter had been changed at 397 hours and the new meter showed 97.1, so just under 500 hours. It was originally ordered as a 1543 per the data plate, and somewhere in it’s life the carriers and tracks had been upgraded to the longer 1600 series versions. SnoTrans sold it to the guy I was buying it from in 2002, and it had the long tracks on it then, so I suspect the upgrade was done during PG&E’s ownership. A couple of bonuses; the Tucker came with a factory installed Warn 8,000 LB winch, and the carriers had the damper wheel upgrade done to them. It had a nice, large rooftop carrier someone had added as well. There were a few repairs that I thought were poorly done, such as a patch on the top of the gas tank, and an ill fitting aftermarket electric fuel pump. But other than that - not bad at all. The paint was original and had 35 years worth of weathering and scratches.
When I was inspecting the machine, the gasoline smelled terrible and the engine had a miss in it. I attributed the miss to either poor fuel, or simply needing a tune up and didn’t think much of it. After buying it, I took it home and cleaned out the inside and then dropped it off at my snowcat buddy’s shop in SLC.
The first order of business was a tune up. The spark plugs looked to be nearly new so we left those alone, but new ignition wires, distributor cap and rotor were installed. And…no change to the miss. So we decided to rebuild the carburetor. In the process we found a significant amount of crud inside and thought that it certainly would run better after the rebuild. And…it didn’t. The next step was a compression check and we found zero compression on two cylinders! How do you have zero? Even if there were holes in the pistons you should see a temporary increase and then a drop. So, off with the valve covers and…the mystery was solved. We found two bent pushrods and two broken rocker arms. I called my “friendly" Dodge dealer and the parts guy only had books that went back to 1985, and he doubted he could get them anyway. Surprising to me, considering how many 318s Chrysler built during the sixties, seventies and eighties. Rather than get some cheap, made-in-China ones, we hit the salvage yards. Believe it or not, finding a 318 or 360 was not easy. Most yards have crushed their older vehicles and focus on newer models. Once the used parts were cleaned up and installed, we started the engine and it ran great. In the carburetor rebuilding process we decided to remove the factory manual choke cable and we installed an automatic choke instead.
Here are some photos of the bent pushrods and broken rocker arms. A couple things to note: For one thing how clean the parts are, indicating low usage and frequent oil changes. The other thing I’d mention is the straighter pushrod was actually much worse. So bad in fact it wouldn’t pull out of the cylinder head without straightening it somewhat.
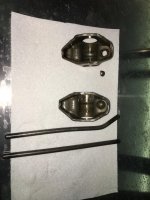
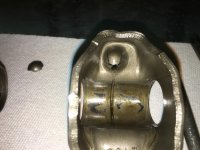
An obvious question is “How did the pushrods get bent and the rocker arms broken?” My understanding is one can bend pushrods at high RPMs if the valves float. But I don’t think that’s the case here. I suspect this sat for a long period of time, the affected valves were closed and they rusted shut. When someone went to start it, the pushrods bent and the rocker arms broke before the valves moved, but that’s really a semi-educated guess.