As we loaded the Imp after our last outing my wife noticed that one of the backing plates was torn loose (a couple of the bolts had broken). She's not a particularly mechanical person, so I was pleased that she noticed something amiss and mentioned it. I guess she's learned a trick or two after being married to an engineer for 30 years.
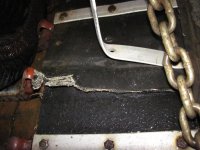
I ordered a bunch of new Grade 8 bolts and nylock washers from McMaster-Carr and today I pulled the cat into the garage and threw it up on jackstands. I replaced the broken bolts and then noticed that a *lot* of the bolts on the tracks were loose. They had nylock nuts so the nuts were tight to the bolt, but you could rattle 30% of the bolt/nuts with your fingers and another 30% spun easily in the hole with a wrench.
I started tightening up the loose bolts while working from the side of the tracks, but it was difficult and uncomfortable reaching the inner half of the grousers -- you had to kneel and reach in through the wheels and across the top of the tracks. It stopped being fun in a hurry.
After a bit I had the bright idea of working from the back of the tracks instead of the side. I was able to set up shop with a bucket to sit on, plenty of light, and all my tools within easy reach. I used a section of pipe as a pry-bar to advance the tracks so that I was able to work on each grouser while it was right in front of me. Still a lot of work, but *way* easier.
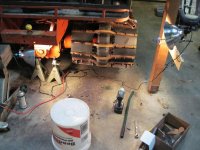
So here's the $10 question -- just how tight are the nuts and bolts on a track supposed to be? "Rattle loose" just seems too loose to me -- the bolts spin and eventually wear through the aluminum backing plates. I'm tightening them till they're moderately hard to twist with a wrench, but maybe that's too tight. So what's your advice?
Thanks
Ron
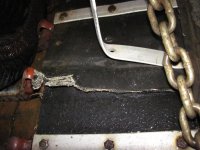
I ordered a bunch of new Grade 8 bolts and nylock washers from McMaster-Carr and today I pulled the cat into the garage and threw it up on jackstands. I replaced the broken bolts and then noticed that a *lot* of the bolts on the tracks were loose. They had nylock nuts so the nuts were tight to the bolt, but you could rattle 30% of the bolt/nuts with your fingers and another 30% spun easily in the hole with a wrench.
I started tightening up the loose bolts while working from the side of the tracks, but it was difficult and uncomfortable reaching the inner half of the grousers -- you had to kneel and reach in through the wheels and across the top of the tracks. It stopped being fun in a hurry.
After a bit I had the bright idea of working from the back of the tracks instead of the side. I was able to set up shop with a bucket to sit on, plenty of light, and all my tools within easy reach. I used a section of pipe as a pry-bar to advance the tracks so that I was able to work on each grouser while it was right in front of me. Still a lot of work, but *way* easier.
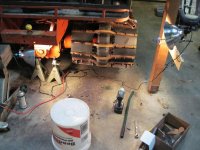
So here's the $10 question -- just how tight are the nuts and bolts on a track supposed to be? "Rattle loose" just seems too loose to me -- the bolts spin and eventually wear through the aluminum backing plates. I'm tightening them till they're moderately hard to twist with a wrench, but maybe that's too tight. So what's your advice?
Thanks
Ron